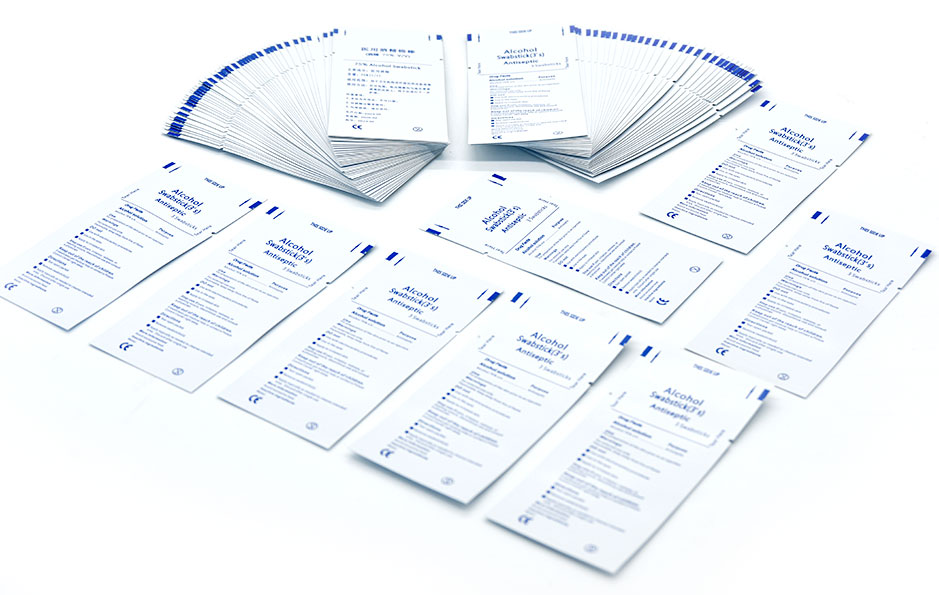
材质 Material:
BOPP/VMPET/PE MOPP/VMPET/PE PET/PE
简介 Introduction
柔印是一种使用具有弹性的凸版的印刷方法,并以其具有良好的印刷质量、适应广泛的印刷材料、较高的生产效率、方便的操作维护、投资少、收益高、符合环保要求等一系列的优点,使柔印成为各种包装产品上选的印刷方案。
Flexo printing is a printing method using an elastic letterpress, and it has good printing quality, adapts to a wide range of printing materials, high production efficiency, convenient operation and maintenance, low investment, high income, and meets environmental protection requirements, etc. A series of advantages make flexo printing the printing solution of choice for various packaging products.
优势 Advantage:
环保要求严格
国家政策引导,倡导“绿色发展”,其主要着力点在于经济发展的方式,即强调经济发展与环境保护之间的协调性,将合理与理性原则贯穿于生产与消费的各个环节,既能使经济快速发展,又能保护生态环境。柔版印刷本身就是一种绿色印刷方式,使用水性、UV、LED UV油墨。
生产效率高
柔版印刷的生产速度通常在100m/min以上,卫星式柔版印刷设备的生产速度在300m/min以上,带有丝印的组合印刷生产速度达60~70m/min,远远高于凸版印刷、间歇胶印等印刷方式的生产速度,生产效率大大提高。此外,一台柔版印刷机通常只需要1~2个人开机,大大降低了人工成本。
调机损耗降低
随着伺服技术和智能控制技术在柔版印刷设备上的广泛应用,以及花瓣式柔印单元的普及,柔印设备的调机时间和损耗成本大大降低。
制版多样化和快速化
随着激光数字制版技术的应用,菲林制版已渐渐退出历史舞台,专业制版公司的制版速度提高,制版费用降低。同时,随着水洗版材的质量不断提高,专业激光制版机的销售费用也大幅度降低,越来越多的标签印企开始自己配备制版设备并制版,使得制版时间和成本大大降低(接近凸版制版成本),适合中小批量订单的使用。
印刷质量大幅提高
数字技术、平顶网点技术的应用,橡胶版的使用,花瓣式柔印单元的普及以及高线数网纹辊的使用都使得柔印质量大大提高,175LPI/200LPI的高网线数印刷已经成为柔版印刷的标准。
投资门槛降低
国内柔版印刷设备生产厂商的技术在不断进步,且销售价格相对便宜,越来越多的标签印刷企业转向投资国内的柔版印刷设备,同时,进口柔版印刷设备生产厂商为了取得更多市场份额,也在降低销售价格,大幅度降低了投资成本。
承印材料范围广
纸张(无论表面光滑或粗糙)、卡纸、瓦楞纸、薄膜、铝箔、软管等复合材料都可以采用柔版印刷方式进行印刷。承印材料范围远远多于平版印刷、凹版印刷、凸版印刷等印刷方式。
色彩一致性强
由于柔版印刷采用短墨路传墨方式,整个印刷过程只包含传墨辊、网纹辊、印版辊和压印辊,且通过网纹辊传墨,可以保证同批次和不同批次印品之间的色彩一致性。
Environmental requirements are strict
Guided by national policies and advocating "green development", its main focus is on the way of economic development, that is, to emphasize the coordination between economic development and environmental protection, and to apply the principle of rationality and rationality to all aspects of production and consumption. The rapid economic development can protect the ecological environment. Flexographic printing itself is a green printing method, using water-based, UV, LED UV inks.
high productivity
The production speed of flexographic printing is usually above 100m/min, the production speed of satellite flexographic printing equipment is above 300m/min, and the production speed of combined printing with silk screen is 60-70m/min, which is much higher than that of letterpress printing, The production speed and production efficiency of printing methods such as intermittent offset printing are greatly improved. In addition, a flexographic printing machine usually only needs 1 or 2 people to start up, which greatly reduces labor costs.
Reduced machine loss
With the wide application of servo technology and intelligent control technology in flexographic printing equipment, as well as the popularization of petal-type flexographic printing units, the adjustment time and loss cost of flexographic printing equipment have been greatly reduced.
Diversified and rapid plate making
With the application of laser digital plate-making technology, film plate-making has gradually withdrawn from the stage of history, and the plate-making speed of professional plate-making companies has increased, and the cost of plate-making has been reduced. At the same time, with the continuous improvement of the quality of water-washed plates, the sales cost of professional laser plate-making machines has also been greatly reduced. More and more label printing companies have begun to equip themselves with plate-making equipment and plate-making, which greatly reduces the time and cost of plate-making (close to letterpress Plate making cost), suitable for small and medium batch orders.
Greatly improved print quality
The application of digital technology, flat-top dot technology, the use of rubber plates, the popularization of petal-type flexo printing units and the use of high-line-count anilox rollers have greatly improved the quality of flexo printing. 175LPI/200LPI high screen-count printing has become printing standards.
Lower investment threshold
The technology of domestic flexographic printing equipment manufacturers is constantly improving, and the sales price is relatively cheap. More and more label printing companies are turning to invest in domestic flexographic printing equipment. The share is also reducing the sales price, which greatly reduces the investment cost.
Wide range of printing materials
Composite materials such as paper (whether the surface is smooth or rough), cardboard, corrugated paper, film, aluminum foil, hose, etc. can be printed by flexographic printing. The range of printing materials is far more than that of lithography, gravure printing, letterpress printing and other printing methods.
Strong color consistency
Since flexographic printing adopts the ink transfer method of short ink path, the whole printing process only includes the ink transfer roller, anilox roller, printing plate roller and embossing roller, and the ink is transferred through the anilox roller, which can ensure the same batch and different batches Color consistency between prints.